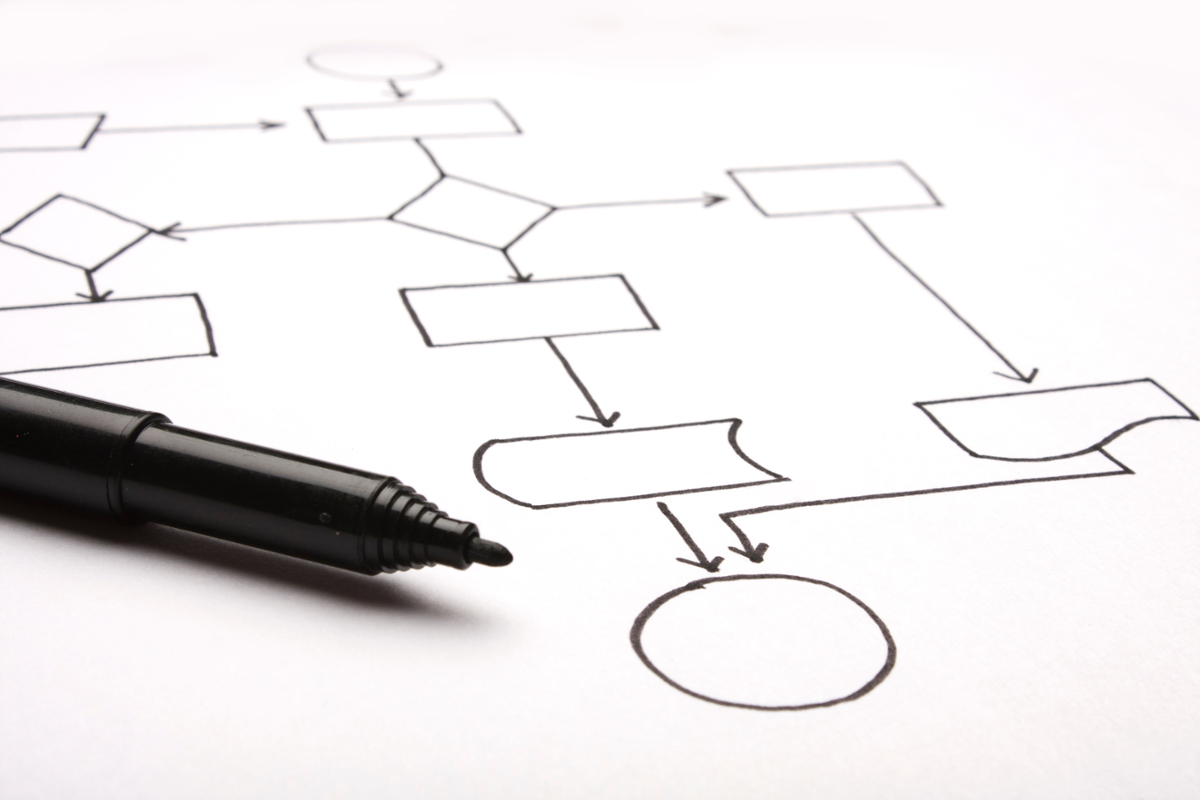
Lean Six Sigma (LSS) Tools
Featured below in various categories are specific tools to help you enhance efficiency and reduce waste. Explore the process improvement tools, templates and examples included.
Process Flow Tools
Process flow tools visually documents a process and helps promote an understanding of current state processes. It further enables teams to identify areas of process gaps, delays, rework loops, etc. that may lead to opportunities for improvement. The following are tips for consideration when using these tools.
- Observe the process: walk the process and talk to the staff to find out what is really going on.
- Involve everyone who is involved in the process or, if not feasible, a cross-representation of all who work in the process.
- Establish practices which make process maps living documents – refer to them in team meetings, use in training and retraining, update with each process change, etc.
- Use current/as-is process map to capture the process as it works today.
- Use ideal/future/should-be process map when a major process redesign is required by asking “what would we do if we could start from scratch?”
- Use updated/to-be process map to describe the new process flow after changes are implemented as part of solution planning or designing/redesigning a process.
The tools listed below provide an overview, tips, example, template, and a short explainer video.
Basic Flowchart (Process Map)
A visual representation of the separate steps and decision points in a process in sequential order. It is a generic tool that can be adapted for a wide variety of purposes, and can be used to describe various processes, such as a manufacturing process, an administrative or service process, or a project plan. Flowcharts are often referred to as process maps; it is important to note that process maps can get much more detailed than flowcharts and can also contain a timeline.
Instructions:
- Review common symbols and meanings.
- Define and title the process to be diagrammed.
- Discuss and decide on the boundaries of the process (start and end).
- Discuss and decide on the level of detail to be included in the diagram.
- Brainstorm as a team the activities that take place. Write each on a sticky note.
- Arrange the activities in proper sequence.
- When all activities are included and everyone agrees that the sequence is correct, draw arrows to show the flow of the process.
Tips:
- A lot of ideas come up when you start creating a flowchart. To keep focused on your primary task, create a “Parking Lot” where you capture important ideas, including process improvement ideas, assumptions, questions, out-of-scope issues, and ideas.
- Transfer the process into a digital format, using MS Word, PowerPoint or any other software using shapes (MS Visio, Lucidchart, Promapp are some options available for an additional fee). We recommend PowerPoint as a free option since you can easily connect shapes with lines and move them around without breaking the connection. You can use the PowerPoint template below as a starting point and modify as you see fit – you can remove shapes and lines or add/modify shapes and lines as needed for your process, using the Insert/Shapes menu in the top navigation in PowerPoint.
Swim Lane
A swim lane flowchart identifies the major functional groups involved with identified activities (the “who” in “who does what”). It makes it easy to study handoffs between people or work groups in a process and identify potential queues, rework loops, etc. It is especially useful with administrative and service processes.
Instructions:
- Review common symbols and meanings. Here’s a link to a step-by-step guide.
- Identify the different people or job functions involved in the process. List them down the left side of a flip chart or whiteboard, creating swim-lanes for the different players.
- Brainstorm the steps in the process and write them on sticky notes.
- Work through each step in order, placing the notes in the appropriate swim-lane.
Tips:
- Use the final swim-lane flowchart to identify opportunities for improving the workflow.
- Avoid repeated handoffs back and forth between individuals or functions. Try to combine or re-sequence work so one person or group can complete all their tasks at once.
- If missing or incomplete information is the source of back-and-forth, try to mistake-proof the process so that work cannot move on to the next step unless complete or accurate to that point.
- Transfer the process into a digital format, using MS Word, PowerPoint or any other software using shapes (MS Visio, Lucidchart, Promapp are some options available for an additional fee). We recommend PowerPoint as a free option since you can easily connect shapes with lines and move them around without breaking the connection. You can use the PowerPoint template below as a starting point and modify as you see fit – you can remove shapes and lines or add/modify shapes and lines as needed for your process, using the Insert/Shapes menu in the top navigation in PowerPoint.
SIPOC Diagram
A high-level 50,000-foot view used to identify the basic elements of a process and stands for supplier, input, process, output, and customer. It is most useful to do a SIPOC diagram at the beginning of the project to capture a high-level view of the process.
Instructions:
- With your team, gather materials and find wall space large enough to accommodate a completed diagram.
- Use 5 sticky notes as headers, one for each SIPOC.
- Begin with the PROCESS first.
- Agree on FIRST and LAST steps of the process first (Use your process boundaries!).
- Fill in the remaining steps of the process in five to eight high level steps.
- Process steps should be a verb.
- One step per note.
- Do not discuss process steps in detail.
- Identify each CUSTOMER of the process and the OUPUT(s) that they received.
- Identify each critical INPUT required and identify the SUPPLIER that provides it.
Tips:
- Be very specific about where the process starts and ends. This should align with the scope of your project.
Spaghetti Diagram
A type of process map, which visually shows the physical flow of work or material in a process. It maps the actual path taken by the workers as they travel through the work area and is named so because the route typically looks like a plate of spaghetti. It is typically used to improve the physical layout of a workspace (office, factory, store, warehouse). It can also be used to depict the flow of information, materials or people.
Instructions and Tips:
- Find or create a diagram of the workspace.
- Work from an existing flowchart of the process steps or brainstorm the list of steps.
- Mark where the first step of the process happens, draw a line to where the second step happens, etc. Continue until you have mapped all the steps.
- Discuss the final diagram with the goal to improve the workflow.
- If the lines crisscross, experiment with workspace arrangements to create a cleaner flow, reduce handoffs and delays.
- If lines repeatedly come back to one location, see if the work performed there could be combined and performed at the same time.
- Prevent backtracking.
Time Observation Sheet
A simple time-based tool to capture “what actually happens” in a process, completed by observing and writing the steps in the process, the running time, notes, and possible types of waste and issues. Observing a process in action creates a deep understanding of reality, helps identify and quantify value and non-value-added steps, and sparks ideas about opportunities for improvement and solutions.
Instructions and Tips:
- Start by clarifying the purpose of observation – is this a general walkthrough or is there a specific purpose (e.g., observing handoffs at a specific step)
- Identify the observers – if possible, include both experienced and novice staff.
- Prepare an observation form (template included below for reference) and train observers in how to use the form.
- Prepare staff in the workplace – alert people in the affected work area about the timing and purpose of observation, get permission from the process owner, supervisor or manager.
- Walk the process and document observations.
- Discuss the results and use as an input to your process improvement project.
Value Stream Map
The purpose is to capture all key flows (work, information, materials) in a process and important process metrics. More complicated to construct than other flowcharts, a value stream map is more useful in identifying and quantifying waste, especially in time and costs. It is often used by busine
Instructions and Tips:
- It is helpful to create SIPOC or swim-lane flowchart first to identify the basic steps.
- Draw the process flow, starting at the end with what’s delivered to the customer and work upstream. Place all activities in a sequence on the map.
- Add the flow of materials, include any inspection and testing materials, add suppliers at the beginning of the process.
- Add the information flow between activities. Document how the process communicates with the customer and supplier. Document how the information is gathered (electronic, manual, etc.).
- Collect process data by walking the process and gathering for each step what triggers it, setup time, processing time, takt rate (rate of customer demand), percent defective or scrap rate, number of people, etc.
- Add process and lead time data to the chart, including delays, processing (value-add) time, setup time, etc.
- Verify the map by having non-team members who know the process review the flow and data.